3. APEX Test Facility Description
The OSU APEX test facility is a one-fourth height, one-half time scale, reduced
pressure integral systems facility. A formal scaling analysis
has been performed to assure that it accurately
models the details of the AP600 geometry including the primary system, the passive safety
systems, and parts of the non-safety grade Chemical and Volume Control System (CVS) and
Residual Heat Removal System. The geometry of the interconnecting pipe routings are also
duplicated. All of the primary system components are fabricated of stainless steel and are
capable of prolonged operation at 2760 kPa (400 psia) and saturation conditions.
Because data from the facility will be used as part of the AP600 certification process,
the applicable sections of ASME NQA-1 have been satisfied
. In particular, requirements for instrument
calibration and records have been established in accordance with Appendix B of Title 10
Part 50 of the Code of Federal Regulations
. Quality assurance (QA) procedures were implemented
in accordance with the Project Quality Plan
. The NRC, Westinghouse QA, and the U.S. Department
of Energy performed facility audits. Numerous safety audits were performed by national,
state and local safety and licensing agencies. General layouts of the APEX facility are
presented in Figure 3-1 through Figure 3-3.
3.1 APEX Primary System
The APEX test facility primary system includes the following components:
- A Reactor Pressure Vessel models the upper and lower reactor internals, the core
barrel, the downcomer and the core. Connections for the hot and cold legs and direct
vessel injection (DVI) lines are provided. The reactor vessel houses 48 electric heater
rods each having a 2.54 cm (1 inch) diameter and a heated length of 91.4 cm (36 inches).
The maximum core power is 600 kW (2.05 MBTU/hr).

|
Figure 3-3. Break simulation piping arrangements overhead
view including Break Separator, Reactor Pressure Vessel, Steam Generators 1 and 2,
and various pipe and break spool configurations. |
- Reactor Coolant Loop Piping
models two primary loops, each consisting of one hot leg
and two cold legs. Break spool pieces are installed on the hot and cold legs, the DVI
line, and the CMT pressure balance line (CMT-PBL) to simulate pipe breaks. The discharge
from these valves vents to the Break and ADS Measurement System (BAMS). The BAMS system is
used to measure break flow rates.
- Two Steam Generators (SGs) , one on each loop, have tube and shell
dimensions scaled to simulate Westinghouse Delta-75 steam generators.
- Four Reactor Coolant Pumps (RCPs) are used two
attached to the lower channel head of each steam generator.
- A Pressurizer (PZR) has internal heaters capable of
controlling pressure and minimizing pressure spikes in the reactor coolant system.
3.2 APEX Passive Safety System
The APEX test facility includes the following passive safety systems:
- Two Core Makeup Tanks (CMTs) each have a pressure balance
line that connects the CMT head to the cold leg. Each CMT also has an injection line that
permits draining of the CMT into one of two Direct Vessel Injection (DVI) Lines connected
to the reactor downcomer. Check valves and isolation valves have been included.
- An In-Containment Refueling Water Storage Tank
(IRWST) has two injection lines that connect to the DVI lines. The IRWST is capable of
being pressurized to 550 kPa (80 psia) to simulate containment back-pressure.
- An Automatic Depressurization System (ADS) includes three
valves on the top of the PZR. The flow from these valves is vented to a sparger inside the
IRWST. The ADS1-3 Flow nozzles are sized to represent two-trains of the AP600 ADS1-3. A
single valve located on the top of each of the hot legs models the fourth stage of the
ADS. The ADS flow nozzles are sized to model two trains of ADS 4 on each hot leg. The
fourth stage ADS flows are vented into the primary sump.
- Two Accumulators (ACCs) pressurized with nitrogen provide safety injection
during depressurization events. Each accumulator has an injection line that connects to
one of the two DVI lines.
- A Passive Residual Heat Removal (PRHR) heat exchanger
is located inside the IRWST. The PRHR is a passive natural circulation heat exchanger
which draws water from a hot leg, rejects the heat to the IRWST, and returns the cooled
water to the cold leg channel of one steam generator.
3.3 Break and ADS Measurement System
The Break and ADS Measurement System (BAMS) is used to measure two-phase flows from
breaks and the four stages of the Automatic Depressurization System
(ADS). The two-phase flow is directed to one of four separators where the flow is
separated into single-phase liquid and single-phase vapor. Since the initial liquid level
in the break separator is equal to the loop seal discharge elevation, the liquid entering
the break separator will displace liquid in the loop seal. The liquid flow through the
loop seal is measured using a magnetic flow meter and directed to the appropriate tank
(IRWST or Primary Sump). The vapor flow from the break and ADS 4 is measured with a vortex
flow meter and vented from the test facility. Vapor flow from the ADS 1-3 separator is
measured and directed into the IRWST. Electrical strip heaters are used to maintain
boundary conditions at approximately 93 ºC (200 ºF). The system is capable of being
pressurized to 550 kPa (80 psia) to simulate containment back-pressure. As partially shown
in Figure 3-4, the BAMS contains the following components:
- A Primary and a Secondary Sump simulate the containment compartment volumes below
the normal flood-up elevation. The sump tanks are capable of being pressurized to 550 kPa
(80 psia) to simulate containment back-pressure. Return lines to the DVI lines are
provided to represent the lower containment recirculation lines.
- Four Moisture Separators are sized based on maximum expected flow rates.
Separation is primarily accomplished by the use of gravity and a swirl vane moisture
separator element. Each separator is provided with a loop seal line on the liquid
discharge to ensure vapor flow does not bypass the separator.
- Containment Sump Return System
provides heated water from a hold-up tank to be
pumped into the primary sump and the IRWST at a mass flow rate equivalent to the mass flow
rate of the vented steam. This heated liquid simulates the flow of condensate from the
steam vented into the containment building. This steam would be condensed and drain into
the IRWST or the containment (primary) sump.
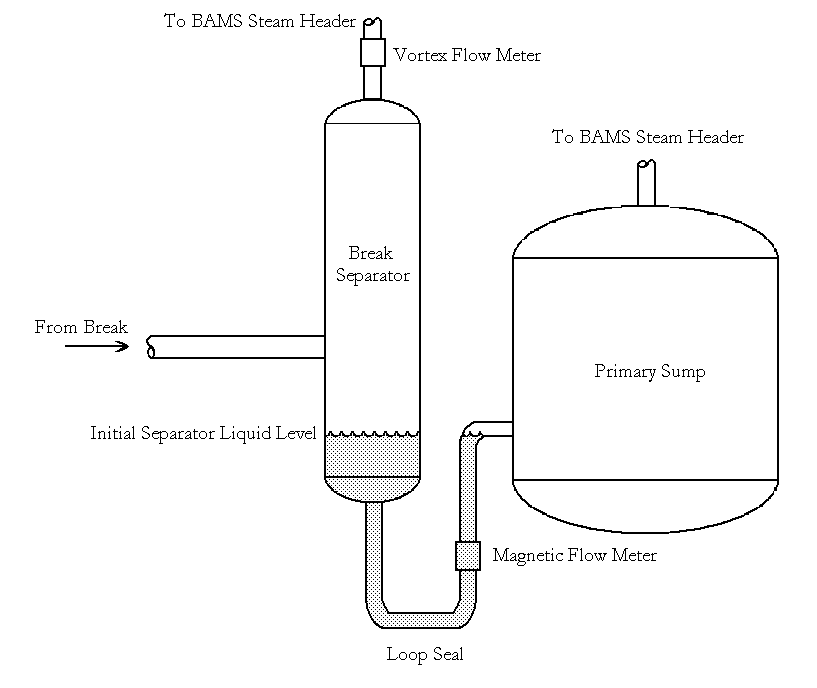
|
Figure 3-4. BAMS general layout for break flow measurements. |
3.4 Instrumentation
Instrumentation is provided to record the necessary data to calculate mass and energy
balances. Approximately 750 channels are continuously recorded by the Data Acquisition
System (DAS). The APEX test facility includes the following types of instrumentation:
- Thermocouples
are used to measure the temperature of the coolant in the primary and
secondary systems, and the supply and component cooling water systems. They are also used
to measure the temperature distribution in the CMT walls and the core heater rods. Premium
grade thermocouples have been used and connected to the data acquisition system (DAS)
through controlled purity thermocouple wire.
- Magnetic Flow Meters
are used to measure all single-phase liquid flow rates.
- Pressure Transducers
are used to measure the static pressures within the various
tanks and vessels.
- Differential Pressure transducers
are used to measure the liquid levels in various
tanks, vessels, and pipes. They are also used to determine pressure drop in system piping
and across various fittings and components.
- Vortex Flow Meters
are used to measure all vapor flow rates.
- Heat Flux Meters
are used to measure heat loss from individual tanks and components.
- Load Cells
are used to measure the weight of liquid inside large tanks.
- Ambient air temperature, humidity and barometric pressure are also recorded.
- All of the instruments are monitored by the DAS, which records the data on computer
files.
3.5 Data Acquisition and Control
The Data Acquisition and Control System (DAS) includes all the
equipment necessary to receive, transmit, process and record the voltage or current signal
outputs from the individual sensing instruments. This includes amplifiers, signal
conditioners, transmitters, interconnecting wiring, analog to digital converters,
interfacing boards, switching panels, computers, displays and other recording devices as
needed to access the instruments. The DAS selected for this project is a FLUKE HELIOS
system linked to three DEC 486 PC Based computers. A Labview software package to process
the incoming data has been developed, validated and fully tested. The DAS is capable of
storing and maintaining all data retrieved and recorded during a single test. The DAS
includes on-line data graphics for process monitoring and a Compact Disk (CD) Writer,
which provides for permanent storage of all test-data on CD.
APEX includes a fully developed control panel capable of modeling all of the important
safety logic of the AP600. All control actions, such as valve openings and closures, pumps
starts, and safety signals are monitored and recorded using the WONDERWARE software
package (same package used for NASA's space shuttle program). This package provides a time
history of all control actions that occur during a test. The WONDERWARE software package
has been fully validated and tested.
